Practical knowledge
The load of a structure generates additional compressive stresses in the subsoil, which are associated with settlements. Under the foundation, the stress distribution takes the form of an onion, which is referred to as a compression onion. The stresses are greatest directly below the base surface. They gradually decrease with increasing depth.
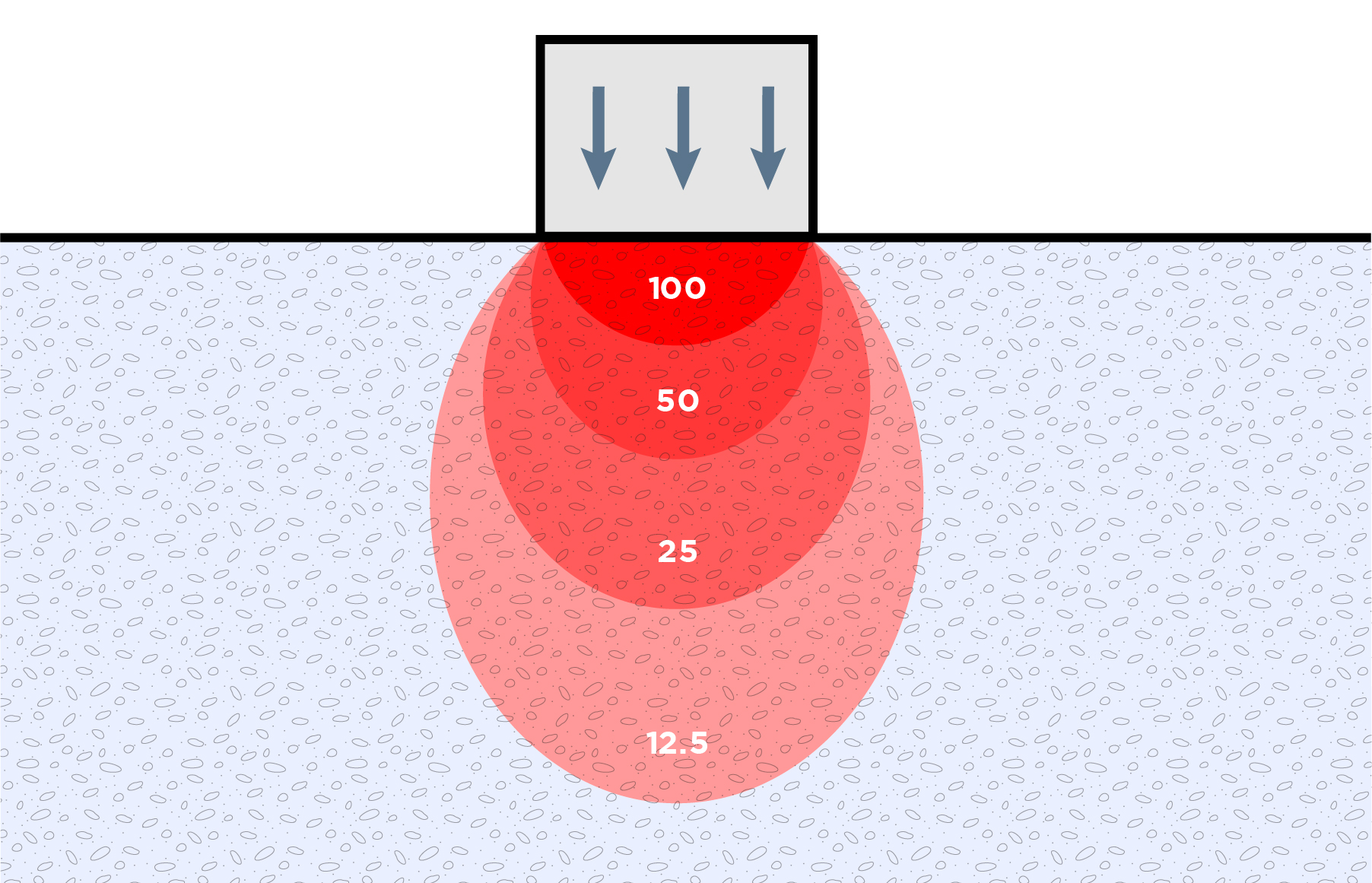
According to the rule of thumb, the effect of the pressure bulb is largely reduced at a depth corresponding to twice the width of the foundation. Consequently, the settlements primarily occur in this zone and the measures to reinforce the subsoil should concentrate on this depth range.